Production Lead Time - As a Custom Sportswear Manufacturer Factory
As a Custom Sportswear Factory, we recognize the significance of efficient production lead times in meeting our clients’ demands and expectations. Our commitment to delivering quality Sportswear promptly is a testament to our expertise, dedication, and operational excellence.
With timelines customized to meet your specific order quantities:
For 600 pcs, we require 10 days.
For 1000 pcs, we require 12 days.
For 2000 pcs, we require 15 days.
For 3000 pcs, we require 18 days.
For 5000 pcs, we require 20 days.
For 10K to 20K, we require 25 days.
For 50K, we require 30 days.
Production time depends on product design and quantity. It’s always changeable.
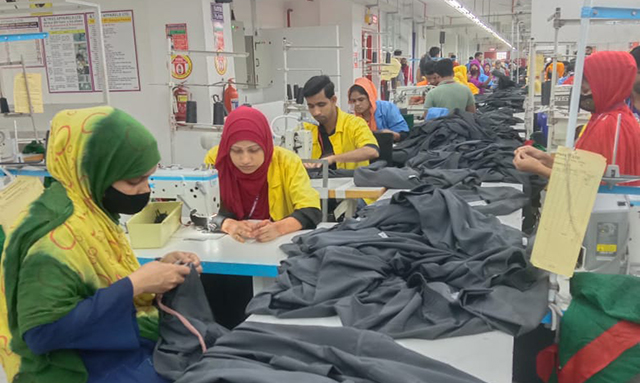
Production Lead Time for Sportswear Manufacturing in a Bangladesh Custom Sportswear Factory
Managing production lead time is a critical aspect of the sportswear manufacturing process. For a Bangladesh Custom Sportswear Factory, efficient production lead time management is essential to meeting client expectations, ensuring top-quality output, and staying competitive in the global market.
Production lead time refers to the total duration from order receipt to the final delivery of products, encompassing steps like design finalization, material procurement, cutting, stitching, quality control, and shipping. Properly managing this timeline allows factories to deliver orders on time without compromising quality. Let’s explore the key factors, challenges, and strategies associated with production lead time in sportswear manufacturing.
Factors Influencing Production Lead Time
Several factors impact the production lead time in a Bangladesh Custom Sportswear Factory, including:
1. Order Complexity
Custom sportswear often involves specific designs, branding, and functional requirements, such as weather-resistant materials or safety features. These customizations demand additional time for design and manufacturing.
2. Material Sourcing
Finding specialized fabrics, accessories, or components required to meet client specifications can delay production. Factories often rely on strong supplier relationships to maintain a steady flow of raw materials, reducing potential hold-ups.
3. Labor and Factory Capacity
Workforce availability and factory capacity significantly affect lead time. During peak seasons or high-demand periods, factories may need to adjust shift schedules or expand the workforce to meet deadlines while maintaining quality standards.
4. Seasonal and Market Demands
Increased demand during certain seasons or product launches can add pressure on production timelines. Proper planning and forecasting are essential to avoid bottlenecks during these periods.
Strategies to Reduce Production Lead Time
Bangladesh Custom Sportswear Factories can adopt several measures to improve efficiency and reduce lead times:
1. Investing in Advanced Machinery and Technology
Using automated cutting machines, computerized sewing systems, and digital design tools can significantly accelerate production. These technologies minimize manual labor, enhance precision, and reduce potential bottlenecks.
2. Streamlining Supply Chain Management
Collaborating closely with suppliers helps factories anticipate material shortages, negotiate faster lead times for fabric delivery, and ensure all necessary components are readily available. A proactive supply chain approach minimizes disruptions and keeps production on schedule.
3. Implementing Lean Manufacturing Principles
Adopting lean manufacturing practices—such as reducing waste, optimizing workflows, and focusing on continuous improvement—can significantly enhance efficiency. This approach not only reduces lead times but also ensures consistent product quality.
4. Resource Allocation and Capacity Planning
Properly allocating resources, such as manpower and equipment, enables factories to handle multiple orders simultaneously. Scaling up operations during high-demand periods ensures deadlines are met without sacrificing quality.
Importance of Communication
Effective communication is a cornerstone of production lead time management in a Bangladesh Custom Sportswear Factory.
1. Client Communication
Maintaining clear communication with clients ensures expectations are well-managed. Regular updates on order progress, proactive discussions about potential delays, and transparent timelines build trust and strengthen relationships.
2. Internal Communication
Strong communication between departments, such as design, production, and quality control, ensures alignment on timelines and priorities. This reduces misunderstandings and delays, resulting in smoother operations.
Why Managing Production Lead Time is Essential
Optimizing production lead time is vital for any Bangladesh Custom Sportswear Factory to remain competitive in the global market. Efficient lead time management benefits include:
- On-time Delivery: Ensures orders are shipped as promised.
- High-Quality Output: Maintains product standards throughout the process.
- Client Satisfaction: Builds trust and fosters long-term partnerships.
- Operational Efficiency: Reduces waste and improves productivity.
By focusing on factors like material sourcing, factory capacity, automation, and communication, a Bangladesh Custom Sportswear Factory can successfully streamline production lead times.
Conclusion
For a Bangladesh Custom Sportswear Factory, managing production lead time is not just about meeting deadlines—it’s about maintaining a reputation for reliability and quality. By investing in advanced technologies, improving supply chain management, and fostering open communication, factories can deliver high-quality sportswear that meets client expectations, ensuring long-term success in the competitive global market.